 |
 |
|
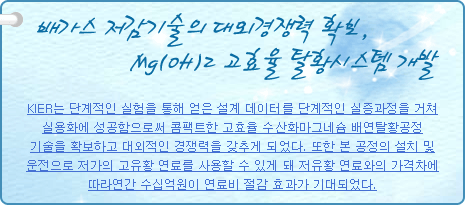 |
|
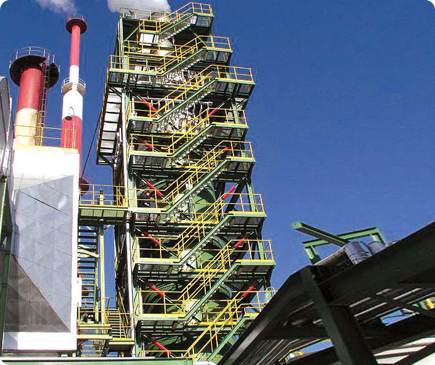 |
|
 |
1990년대 이후 우리나라는 지속적으로 국내 환경규제 기준이 강화돼 일부 대기환경 규제의 경우 선진국 수준에 근접 하기에 이르렀고, 지방자치단체에서도 규제 강화 방침을 밝히면서 강력한 실천 의지를 보였다. 이에 대표적인 배가스 대형 배출원인 국내 화력발전소들을 중심으로 배연탈황 설비들이 설치되어 운전되기 시작했으며, 이어 열병합발전소 및 금속제련소 등에서도 배가스 처리를 위한 다양한 규모의 배연탈황공정들이 운전되었다. 그러나 기존의 대형 배출설비에서 사용되고 있는 배연탈황공정은 대부분 석회석을 알칼리 반응제로 사용하여 배가스 중 황산화물을 흡수 중화 처리한 후 석고를 부산물로 생산하는 습식 석회석-석고 공정이었다. 이 같은 습식 석회석-석고 공정은 운전비용이 비교적 저렴한 반면 반응제인 석회석의 가공·저장 시설 등 초기 투자비가 크고 용수 용량이 많은 단점이 있었다. 더구나 운전부하가 수시로 변하거나 주말가동이 정지되는 산업체의 경우에는 일정한 탈황효율이나 탈황석고의 품질을 유지하기가 쉽지 않았다. |
 |
이에 따라 울산석유화학지원공단, 쌍용정유, LG금속 등 국내 대형 산업체에서는 배연탈황시설을 설치하면서 습식 석회석-석고 공정 대신 Mg(OH)2를 알칼리 반응제로 사용하는 배연 탈황공정을 적용하게 되었다. Mg(OH)2를 이용한 배연탈황공정은 석탄이나 중유를 사용하는 산업체의 연소설비나 배출설비의 배가스에 포함된 아황산가스를 선택적으로 제거하기 위한 기술로서, 반응기 내에서 수산화마그네슘 알칼리 용액을 분사하여 배가스에 포함된 아황산가스를 흡수한 후에 산과 알칼리의 중화반응 및 산화반응을 통해 정화된 배가스를 굴뚝으로 배출시키는 시스템이었다. Mg(OH)2 배연탈황공정은 시스템 구조가 간단하고 설비규모가 작아 초기 투자비가 절감되며, 탈황 후 용해도가 높은 MgSO4가 생성되므로 고체슬러리의 발생이 억제될 뿐 아니라 처리비용도 적게 소요되었다. 또한 순환용액 중 고체함량이 낮기 때문에 배가스의 성상에 따라 다양한 충전탑을 사용할 수 있는 장점이 있었다. 그러나 이 시기에 우리나라는 이러한 공정기술 대부분을 일본에 의존하고 있었기 때문에 설비 건설 시 많은 기술료를 일본에 지불해야만 했으며 공정 운전 시 문제점이 발생할 경우 이를 해결할 자체기술력을 확보하지 못하고 있는 실정이었다. 이에 더해 향후 중국의 환경시장 진입을 고려할 때 국내에서 자체 개발된 탈황공정기술이 절실히 요구되었으며, 이 같은 시점에서 KIER가 배연탈황공정 연구를 수행하게 되었다. |
 |
KIER의 초기 연구는 당시의 습식 석회석 공정이 가지고 있는 낮은 SO2 제거효율과 흡수탑 내의 scaling 등의 문제를 해결하는 데 초점을 두고 진행되었다. KIER는 기술 개발을 위해 우선 국내 배출설비 현장의 운전데이터와 문제점 등을 광범위하게 조사했으며, 이를 근거로 실험실에서의 각종 실험과 단계적인 입증절차를 거쳐 기존의 탈황공정에서 발생할 수 있는 문제점들을 획기적으로 개선하는 데 기여하게 되었다. 기존의 습식 석회석 공정에 첨가제로서 Mg 화합물을 주입하는 공정은 1973년 일본의 Kawasaki 중공업(KHI)에 의해 처음 개발되었는데, 이러한 기술을 바탕으로 1998년에는 Mg(OH)2를 배연탈황용 알칼리 반응제로 이용하여 SO2를 흡수하고, 반응생성물은 산화과정을 거쳐 고용해도의 수용성 MgSO4로 배출하는 배연탈황공정을 개발하게 되었다. 공정 개발을 위한 연구 단계에서는 Mg(OH)2와 SO2의 반응성 측정실험을 수행하기 위한 실험실 규모의 실험장치를 제작, 운전했다. 연소가스 150m3/hr을 처리할 수 있는 벤치(Bench) 규모의 FGD장치를 제작하고 각 유니트(unit)별 특성실험 및 운전변수에 따른 최적 조업조건을 선정했다. 또한 흡수탑 내의 충전물 특성을 파악하기 위하여 스프레이 타워(Spray Tower), 제1부 대한민국 에너지사에 남긴 빛나는 업적 167 TCA(Turbulent Contacting Absorber), DFT(Dual FlowTray), CDFT(Cycloyd Dual Flow Tray)를 제작하여 각각의 성능을 비교한 결과, CDFT를 이용하여 98% 이상의 SO2를 제거 할 수 있었다. 본격적인 공정연구로는 KG 케미칼(주)과 함께 Mg(OH)2를 이용한 고효율 탈황공정의 개발이 착수되었다. 온산의 KG 케미칼(주)에서 운전 중인 10톤/hr 규모의 보일러 연소가스를 처리하기 위한 3MW급 파일럿 플랜트(Pilot Plant)를 설치하고, 장치의 성능점검 및 보완작업을 통해 각 공정의 문제점 해결과 함께 장치의 신뢰성을 확인했다. 이어 연속운전 실험 및 최적 조업조건을 도출하기 위한 운전변수별 특성실험을 수행함으로써 운전기술까지 획득하여 완성도 높은 기술이 탄생하게 되었다. 나아가 3MW급 파일럿 플랜트에서 확보된 운전 데이터 및 운전기술, 구성 장치 및 부품에 대한 노하우를 바탕으로 추진력을 더욱 높여 대형화된 플랜트의 설계기술을 확보했다. 기술 개발이 완료된 후에 KIER는 한라산업개발(주)과 함께 전남 대불공단 내 보워터한라제지사의 100t/hr급 스팀공급용 보일러의 배연탈황공정 설계를 수주하여 2003년 12월에 성공적으로 준공함으로써 설계기술력을 대외적으로 입증하였다. |
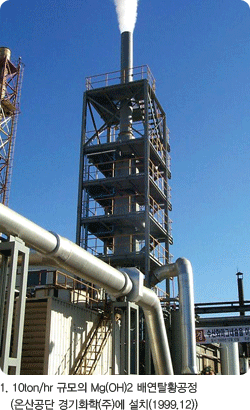 |
 |
KIER는 단계적인 실험을 통해 얻은 설계 데이터를 단계적인 실증과정을 거쳐 실용화에 성공함으로써 콤팩트한 고효율 수산화마그네슘 배연탈황공정 기술을 확보하고 대외적인 경쟁력을 갖추게 되었다. 또한 본 공정의 설치 및 운전으로 저가의 고유황 연료를 사용할 수 있게 돼 저유황 연료와의 가격차에 따라 연간 수십억원의 연료비 절감 효과가 기대되었다. 한편 KIER의 기술 실증 파트너인 KG 케미칼(주)은 온산의 LS-Nikko 동제련(주)(구, LG-Nikko 동제련)의 동제련로 폐가스 처리를 위한 배연탈황공정(가스처리량 12만 5000Nm3/hr, 증기발생량 환산 125톤/hr)을 수주하여 2004년 말 탈황효율 97% 이상으로 운전에 성공함으로써 수산화마그네슘을 이용한 배연탈황공정의 설계 및 시공 기술에 대해 확고한 위치를 확보 하게 되었다. |
 | |
|
본 메일은 발신전용메일로 메일수신을 동의하셨기에 기재해 주신 이메일 주소로 발송되었습니다. 한국에너지기술연구원에서 드리는 각종 정보의 메일 수신을 원치 않으시면 [수신거부]를 눌러 회원 개인정보를 변경해 주시기 바랍니다. If you do not want this type of information or email, please click here  기타 문의 사항은 한국에너지기술연구원 웹사이트의 [ 참여마당> 묻고 답하기 ] 메뉴를 이용하여 주시기 바랍니다. |
  | |